Turbine Maintenance –
LM2500 and LM6000
Increase Turbine Service Life
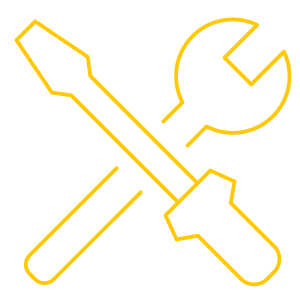
Maintenance programs extend the service life of your turbine, ensures optimal efficiency and reduces critical disruptions in your operations. In addition to reducing the total cost of ownership, programs can deliver lower cost on replacement parts for critical components.
United Power’s engine overhaul services include component and module repair for the entire product line of turbines and packages. All turbines are run in a test cell for output, vibration, oil consumption and horsepower output.
With more than 500 installed locations, our equipment operates in challenging conditions around the globe. To support you, field service technicians are available worldwide to perform on site analysis and maintenance. Every technician is trained and certified to deliver quality service for our complete line of gas turbines.
Our maintenance program includes:
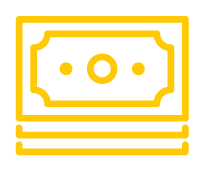
Sale, lease, and exchange programs for complete turbines
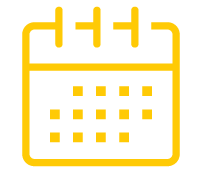
Distribution of New and Overhauled Parts
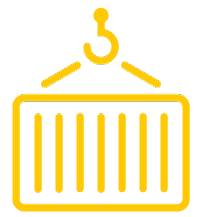
Repairs, overhauls and exchanges of turbine components and modules for the United product line
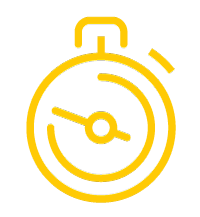
Specialized inventory management for provisions on a just-in-time basis, worldwide.
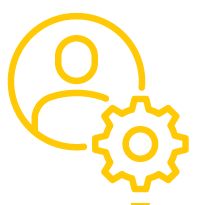
Repair facility for all parts, components, modules, power turbines, and entire turbines
Complete Operations and Maintenance (O&M) Capabilities Worldwide.
One of the biggest O&M expenditures is the fixed cost associated with day-to-day preventative maintenance and the variable cost for corrective maintenance and parts. To help improve the cost structure, United Power’s global footprint of inventory supply, field service and parts certification delivers greater O&M assurance.
Our O&M capabilities include:
In addition to maintenance we can reduce costs in other parts of your turbine operation. For example, our service staff and part sourcing ability delivers the highest quality components cost effectively so you won’t pay traditionally high OEM prices. Our exceptional exchange program saves customers more than 75% below OEM spares prices while substantially reducing down time.
You can also manage costs with the best turbine warranty in the industry. It includes a long term service program, technical standard order (TSO) and covers one year or 8,000 fired hours.
One of the biggest O&M expenditures is the fixed cost associated with day-to-day preventative maintenance and the variable cost for corrective maintenance and parts. To help improve the cost structure, United Power’s global footprint of inventory supply, field service and parts certification delivers greater O&M assurance.
Our O&M capabilities include:
- Turbine repair and overhaul services to limit equipment downtime
- Service contracts to deliver long term maintenance
- Certified replacement parts at a cost 75% lower than OEM prices
- Warranty of one year or 8,000 fired hours from start or 18 months from shipment.